Please note that while the text is from 1914, some of the photos show later model automobiles. Also, as the pictures are from multiple vintage sources, they don’t necessarily demonstrate the sequence of actual manufacturing, nor do they always match the nearby text. But we tried!
In 1908, Henry Ford introduced the Model T, and the Tin Lizzie caught the fancy of the nation. The Automotive Age had begun full throttle. Ford had to expand his facilities to supply the demand for the Model T.
In 1910, he opened a new plant in Highland Park, Michigan. The following year, the first branch plant in the industry was opened by Ford in Kansas City, Missouri. But the slowness of production nagged at Ford. To speed things up, he portioned out the jobs in the assembly work and scheduled parts to arrive at the workers at given times.
Finally, the moving assembly line evolved, and mass production was a manufacturing fact of life.
The early Tin Lizzies spent 12 hours and 28 minutes being assembled. The time was chopped to 5 hours, 50 minutes, and eventually, the Model Ts rolled from the lines at a rate of one every 10 seconds of the working day. – Excerpted from The Boston Globe (Boston, MA) July 28, 1963
Inside the Ford factory producing Model T automobiles on assembly lines (1914)
Text excerpted from Automobile Trade Journal, Volume 18 (1914) – Photos from multiple sources
The Ford Motor Company, Detroit, Michigan, can justly claim high position among the leading industrial successes of the entire world, both in total number of persons dependent on its activities for subsistence, something like a total of 250,000 individuals deriving support from the Ford Company earnings, and in the volume of profits in ready money constantly flowing into its treasury, and at the same time the Ford Company has the unique distinction of offering but the one single article of sale to purchasers.
The sole commercial product of the Ford Motor Company is Ford Model T Cars, all having the same chassis, and varying from each other only in the form of body mounted thereupon.
Yet the Ford Motor Company is now by far the largest and wealthiest and in every way the most successful motor car build ing concern in the world, earning profits of from ten to fifteen millions of dollars yearly, and turning out more than a thousand new Ford cars as its regular day’s work.
The original Ford assembly lines
The visitor approaching the Ford plant at Highland Park for the first time is impressed by the great extent of the buildings, and has the sense of plunging into a swift and urgent current of earnest business as the door opens to give admittance to the Foyer, with a marble stairway leading to the upper floors on the far side, elevator doors and a Ford car at left of the stairway and the Information Desk at the right.
On either hand long vistas of corridors between rooms occupied by officials and their assistants, and notes, perhaps with some surprise, that no old, or even elderly men are anywhere visible. This is one of the marked characteristics of the Highland Park plant officials; all are young for their positions, all without exception are in the prime of life, and all give the impression of exceptional power and intelligence.
This characteristic of youth extends to the worker as well as the officials of the Ford Company, and men and women alike, with but very few exceptions indeed are on the fortunate side of middle age. The machine shop superintendent’s office is on the left and some of the tool-makers are seen working at the right, with the first floor doors of the factory passenger elevator, an extremely busy vertical travel duct which averages 500 passengers carried per hour.
Reaching the fourth floor and walking northward, the radiator department opens to view with a long horizontal belt for radiator transportation in the foreground, one of many endless belt and endless chain transmissions employed in these shops to lessen travel and transportation costs and delays as much as may be.
Indeed, it may be justly said that the most important and the most difficult problem which has confronted the Ford engineers from the time of the first work at Highland Park to the hour of this writing, has been the transportation of men, materials and work in progress from one location to another on the Ford plant premises.
The importance of this one item of transportation improvement can be comprehended when it is known that the seemingly unimportant conception of the idea of moving motors while under assembling operations by sliding them along on pipeways, reduced the force of motor assemblers needed to produce 1000 motors per day from 1100 to 500, with no very marked changes in the motor assembling routine.
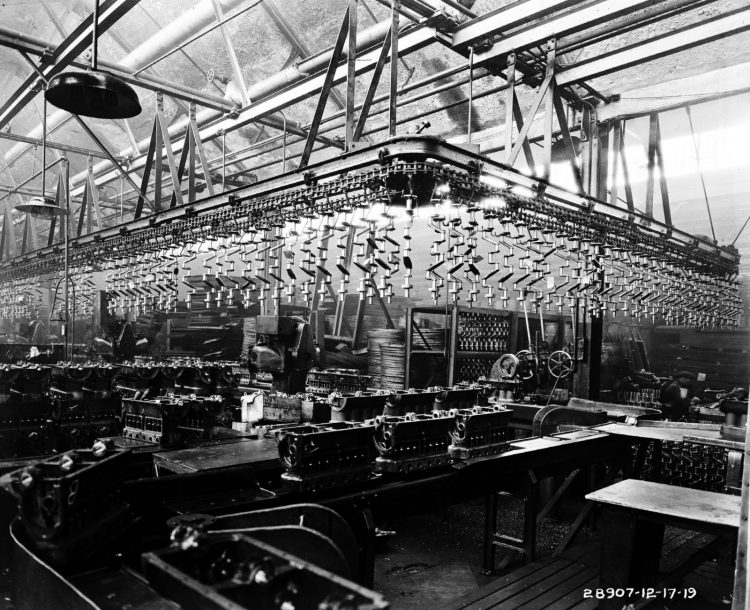
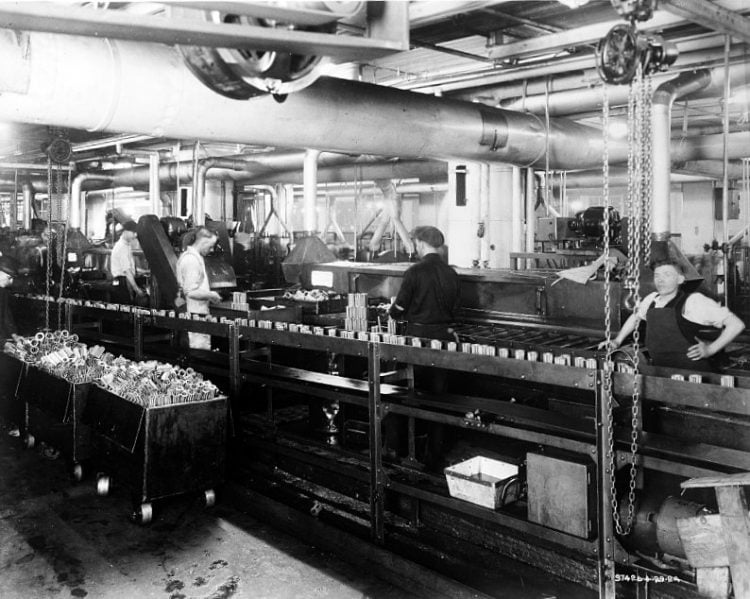
This digression caused by sight of the endless belt does not in the least interrupt the construction activities of the 450 workmen employed in assembling, soft-soldering, testing for leaks and cleaning the 1000 radiators per day which they turn out.
All hands are seen to be diligently engaged in carrying on the myriad of detail operations needful to complete the Ford radiator, made in the highest style of radiator construction, tested to absolute certainty of perfect workmanship at every point and produced at a flat cost of $7 each, although the Radiator construction is aided by a plant of special tools and fixtures covering every production operation in the fullest manner conceivable.
The Ford Radiator is all of brass and is contrived and put together in the manner best calculated to give strength to that soft soldering which seems indispensable to the highest efficiency for weight.
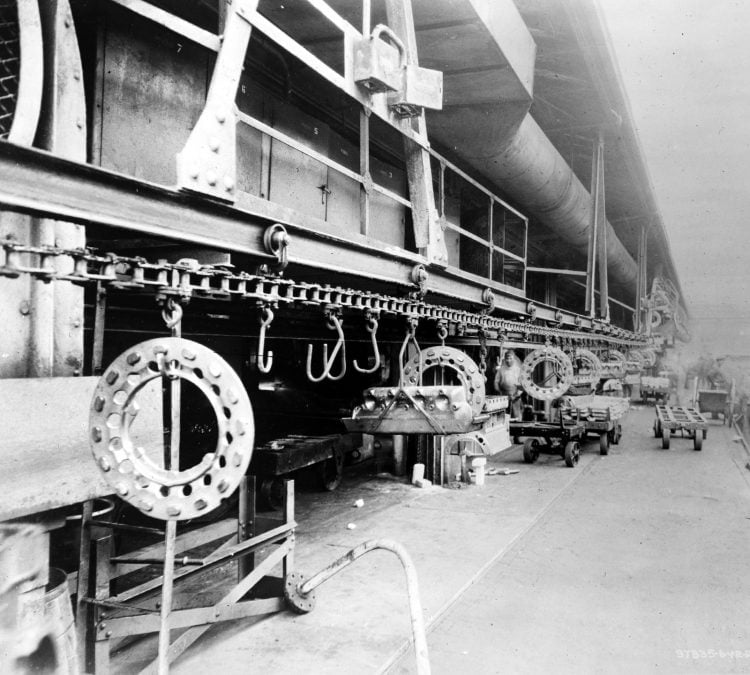
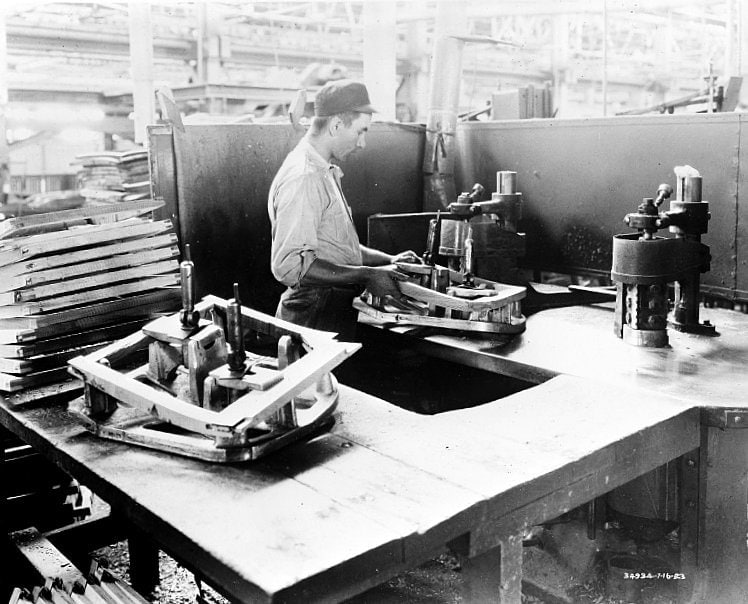
Walking back to the southward the radiator painting is passed on the right and left, and next comes the body upholstering on the right and the upholstering stock room on the left side. Turning at a right angle and walking eastward the visitor passes an enormous stock of obsolete parts, which must be carried as repairs and replacements because hosts of early model Ford cars are yet in active commission.
Next on the right is the coil box gaging and coil testing department. The coils are supplied by three makers, the K-W Ignition Company, Cleveland, Ohio; the Heinz Electric Company and the Kokomo Electric Company. The coil boxes are now made by the Ford Company. The testing to which each coil is subjected to ensure its perfect operations in the vitally important function of charge-lighting is thorough.
Ford assembly lines: Mufflers, wheels, tired, windshields
Yet to the eastward lies the muffler department, followed by the beginning of the fender job floor. Turning to the northward, the fender painting floor is passed, and then follows the gasoline tank department; next the motor hood painting, and finally, at the north end of the eastern section of the third floor, comes the fender dipping in Japan varnish on the left and the fender baking ovens on the right.
Descending to the third floor the visitor walks to the southward with the wheel painting floor on the right and the wheel and tire assembling on the left.
Passing yet to the south the windshield and floorboards departments are passed and then, facing westward, the brass bush finishing and storage departments are found to occupy the entire third floor, Manchester Street side.
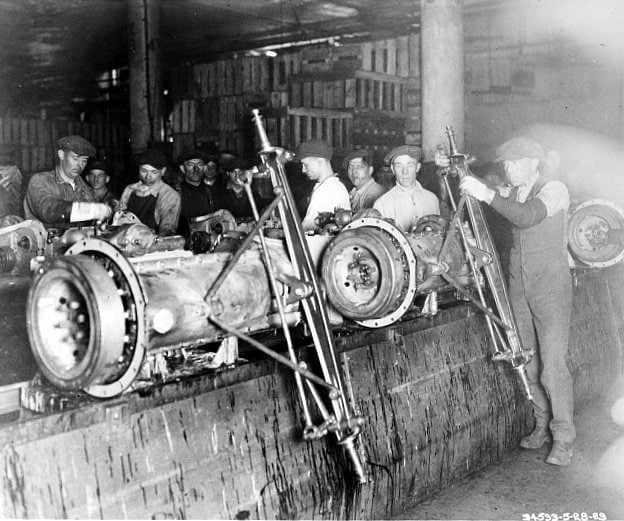
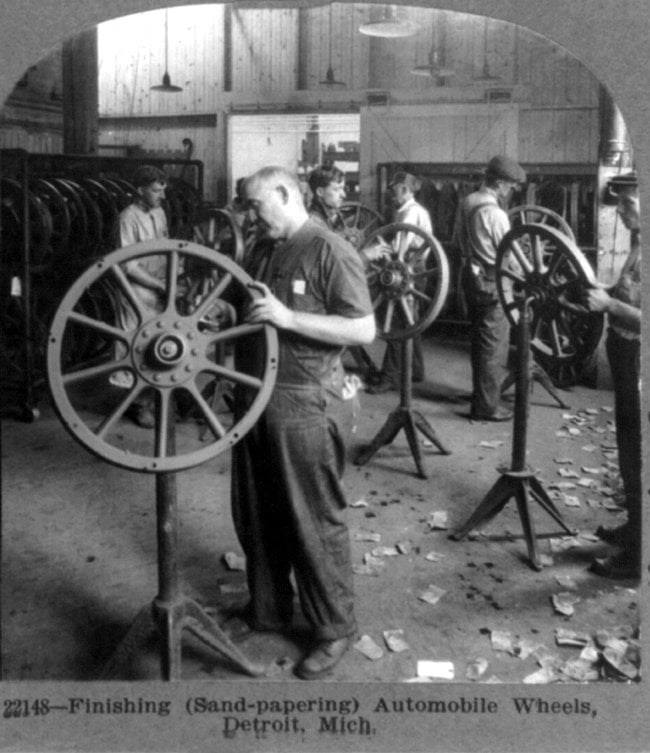
Turning and facing north the body making, body painting and body trimming departments are passed. Then come the upholstering sewing machines on the left and right, followed by workbenches thickly lined by girls who make the magnet fields and the wiring and the repair kits… Then follow the magneto and commutator finishing and assembling, with related storerooms at the north end.
The metallurgical lab and the Ford assembly lines
Descending to the north end of the western side of the second floor, and facing to southward the visitor walks the length of the shipping room, a department of the highest commercial importance, but exhibiting only the most commonplace of pictorial effects, and then, entering a door at the left, the metallurgical department is disclosed.
In the Metallurgical Chemical Laboratory and Heat Treating Department, test pieces from every ingot of steel used to form Ford car components undergo tests for strength and analytic operations which show the chemical constitution in detail, things which must be known before any motor car steel component can be intelligently heat-treated, or safely put at work on the road.
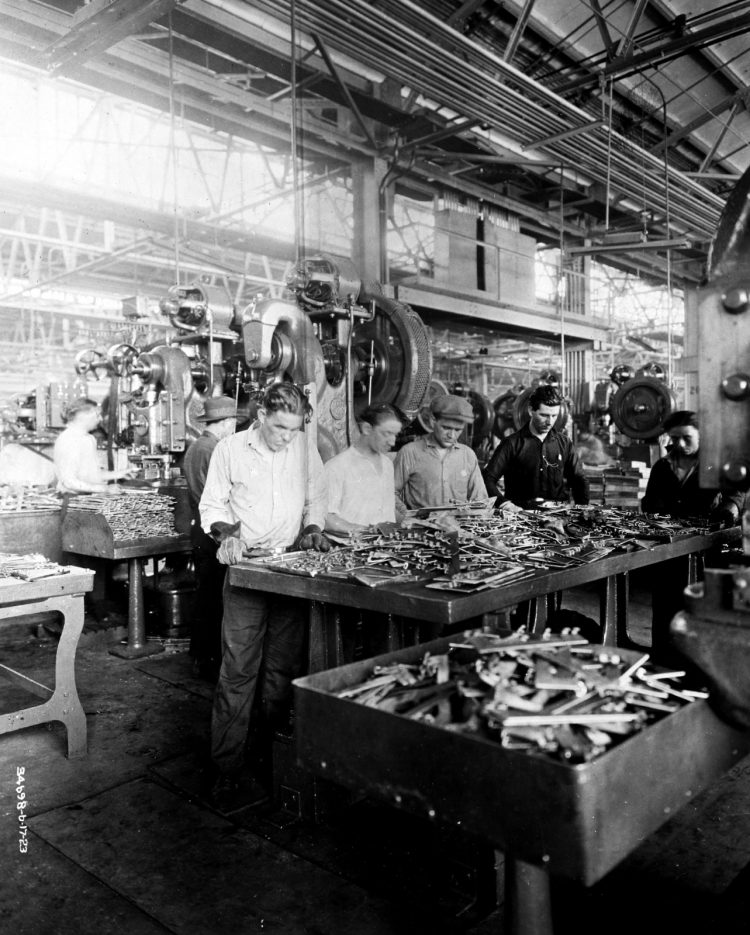
The Ford Company’s chemical laboratory is operated by one head metallurgist and six assistants. The heat-treating department is in charge of one head, who gives specific orders as to all details of actual operations in the heat treating department.
The actual heat-treating department, equipped with furnaces, steam hammers for straightening pieces after heating and quenching, with cooling baths and a large force of skilled furnace tenders and workmen, is in charge of one head, who is constantly advised of the actual temperatures of his numerous furnaces by a force of skilled temperature observers, located above one of the hospital first-aid stations, in close proximity to the heat treating working floor.
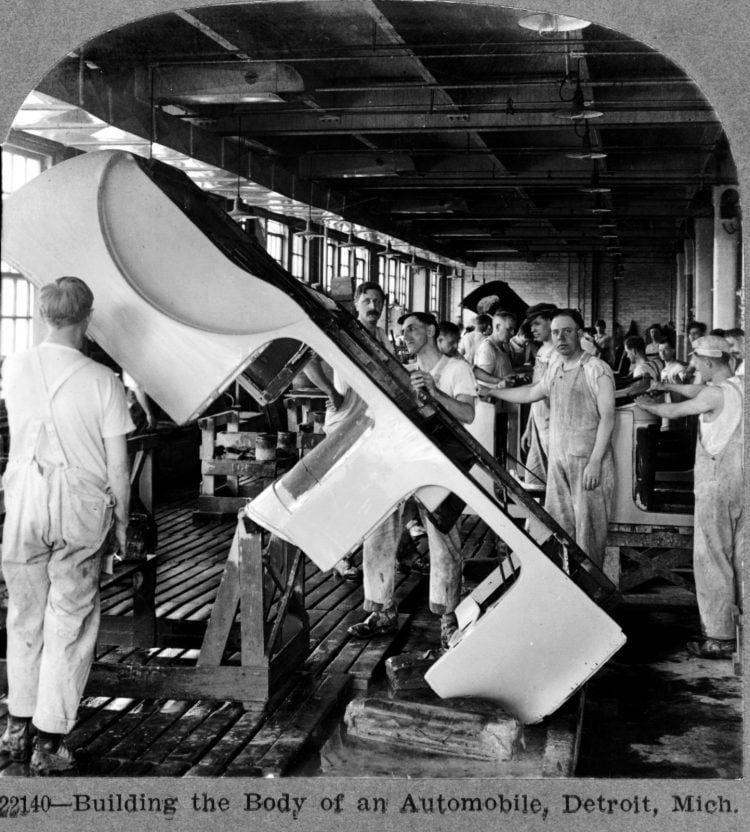
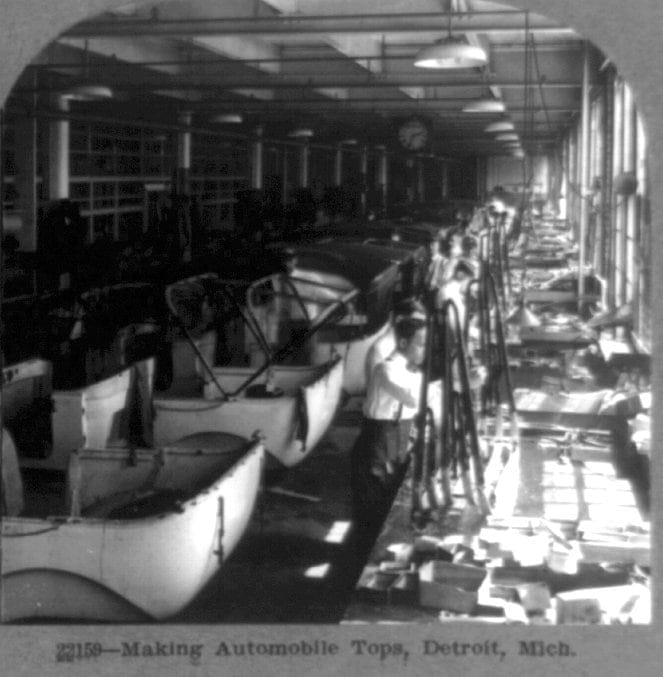
Costly pyrometers, connected with individual furnaces, continuously announce furnace temperature variation by different colored lights placed in front of the temperature observers, who note important temperature variations and report by telephone or by pneumatic tube message carrier the furnace tenders who increase or decrease the heat of any individual furnace as may be needed to keep it within 5 degrees F, above or below the temperature designated for the particular service of a given individual furnace.
Turning into the north side machine floor passageway the screw machines are passed on the left, with drill presses and the cone department on the right, and crossing the traveling crane way gives a long perspective of material in plentiful piles and stacks as far as the eye can reach.
Beyond this is the power house, No. 2, containing a number of dual units each consisting of a motor driven by Edison alternating current, fixed to the same shaft with a direct current producing dynamo.
Direct current generated by the dynamos goes to the switchboard, where it is diverted to the motors driving the shafting in the various departments throughout the plant, this power house being used in connection with power house No. 1, on Woodward Avenue, where the big Hamilton-Gray motor is located. The switchboard in power house No. 2 is, of course, so constructed and arranged as to either drive or stop any line-shaft-driving motor in the entire plant, so that no shaft is turned when not needful.

Three artesian wells at the south from of power house No. 2 furnish water for shop use to a pumping engine, which supplies the large elevated tank located near the northern end of power house No. 1, that forms a prominent landmark in the Ford Plant pictures.
Turning south on John R Street, for a short distance, the railway freight cars’ unloading platform is reached, which extends for about 1000 ft. eastward to the end of the foundry, with the freight cars and the blacksmith’s department, or heat treatment No. 2, on the south.
This department being known by both names is on the north side of the freight unloading platform, which shows a scene of great activity, as all of the metal rough stores, sheet and bar steel, drop forgings and components from outside suppliers are here taken from the freight cars, two trains per day, and counted into various shop transportation receptacles and removed by truckmen or by the monorail line, which serves the entire length of this train unloading platform.
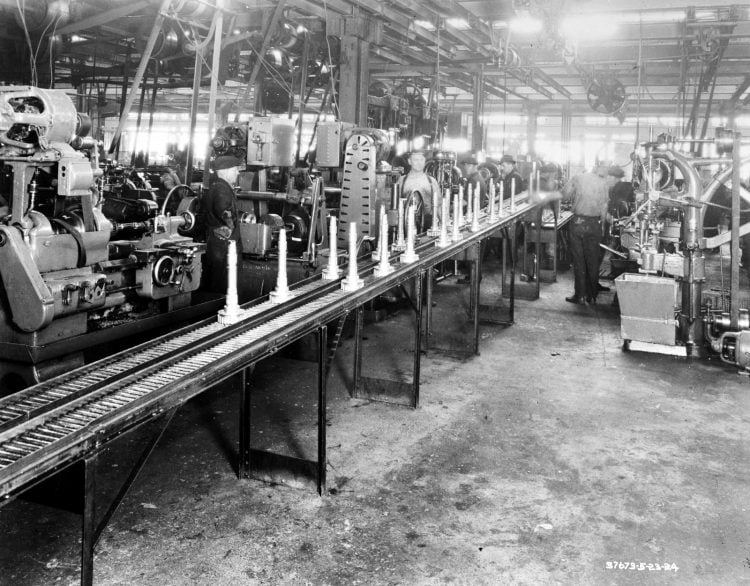
Walking eastward through the smithy, steam hammers and smith’s forges come first, then the furnaces, which heat, and “bulldozers,” and cut off and bend the flywheel magneto magnets and heat them afterward for hardening, followed by the rear axle sleeve forming plant, which includes a picturesque application of oxygen blow-pipe brazing.
To the eastward of the rear axle tube forming plant the aluminum castings crank box covers are cleaned and “patched” by soldering, an operation always practiced in the production of large aluminum castings having very thin walls.
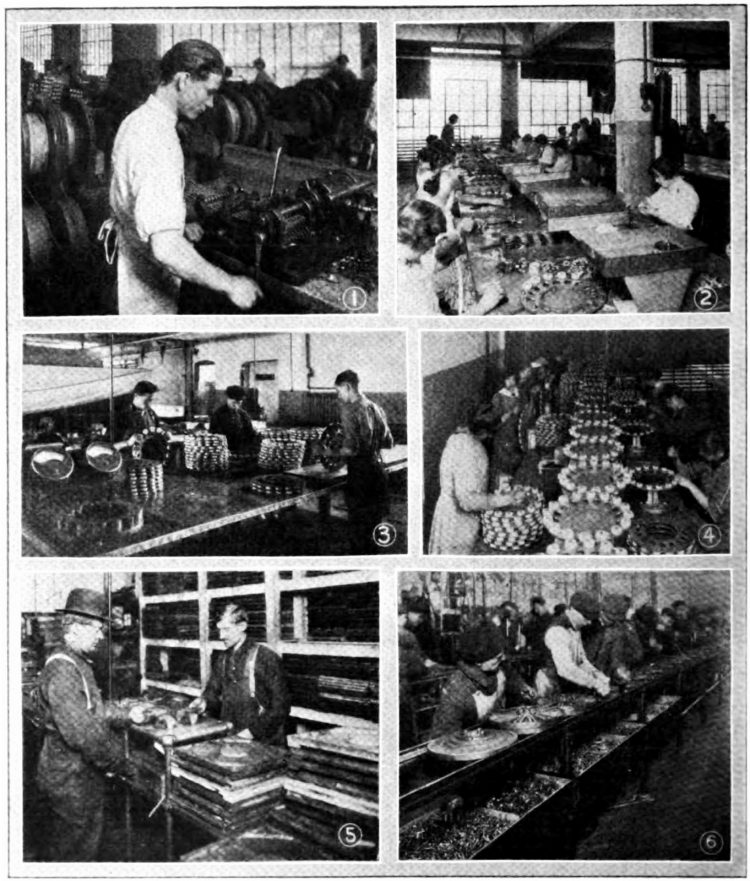
Passing the comparatively small aluminum foundry floor at the east end of the smithy the Gray Iron Foundry, working 1600 bands, is reached.
This foundry is said to employ a more highly developed system of sand conveying, mixing and delivering, of mold-transportation to the pouring point, near the big ladle line from the cupolas and thence back to the “shake out” over sand conveyors underneath the floor, and core sand mixing and delivering scheme for supplying the carmakers, than any other gray iron foundry in existence.
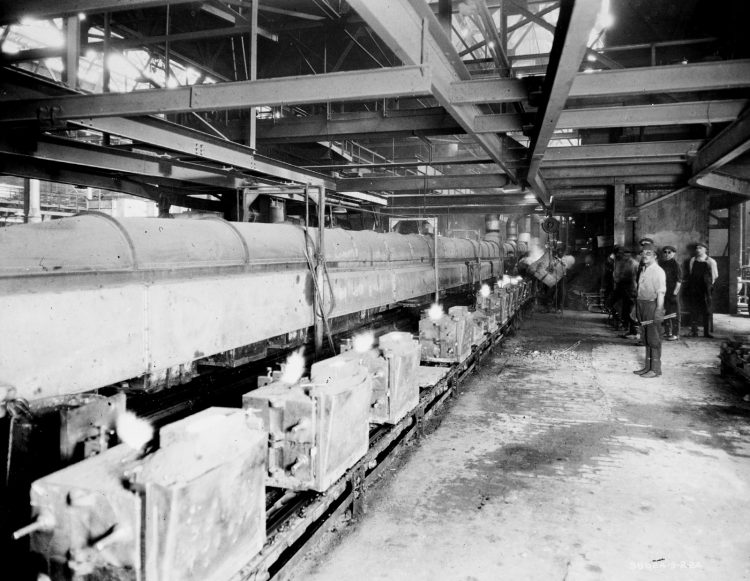
Both the machine molders and the core makers have overhead chute sand supply, and the machine molders stand underneath an endless chain sand conveyor, and also stand above the same endless chain conveyor, located beneath the floor and having one end of the endless chain sand conveyor circuit carried upward to supply a sand cutting and mixing and dampening trough.
There, the sand, yet warm from the “shake-out” table is cut over and automatically moistened, and then is carried back again over the machine molders’ heads to supply the elevated sand chutes, in endless circuits.
Ford assembly lines: Engine and auto chassis
Then, turning to the northward on the John R Street side of the factory floor a short walk brings the busy scene of the chassis assembling lines south end into view, a scene of intent and multitudinous effort without a parallel in any other automobile factory on earth.
Here the chassis frames shirt to the eastward from the springs and chassis frame assembling lines, and successively receive the axles, the wheels, the motors, the mufflers, and the dash and steering gear assembly, each assembled component delivered to the chassis assembling line from overhead receiving stages, galleries or chain hoists as the case may be, the lines of chassis frames slowly moving to the northward.
They are attended at every point of component reception by a group of specialist toilers who unite each newly received member of the growing chassis assembly to the chassis frame as received, and in turn passing the partly completed organization forward to the next group at the next component receiving station.
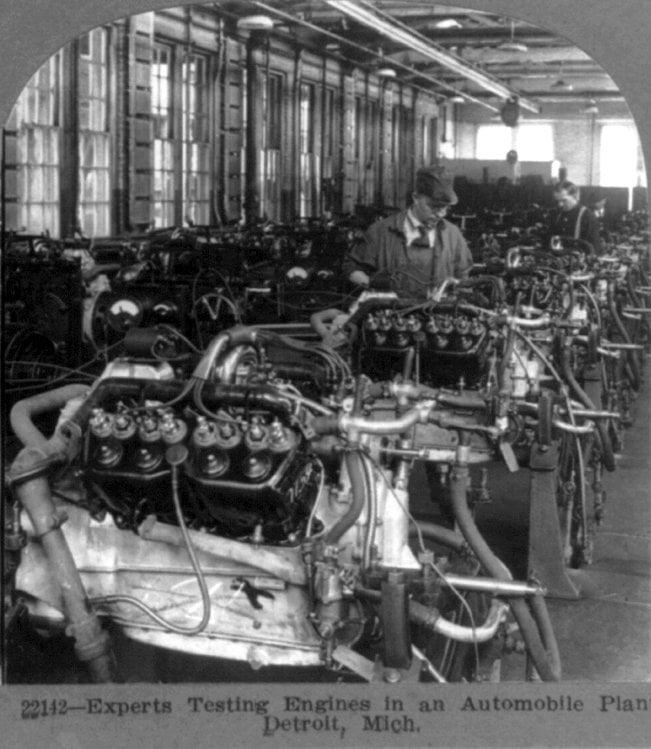
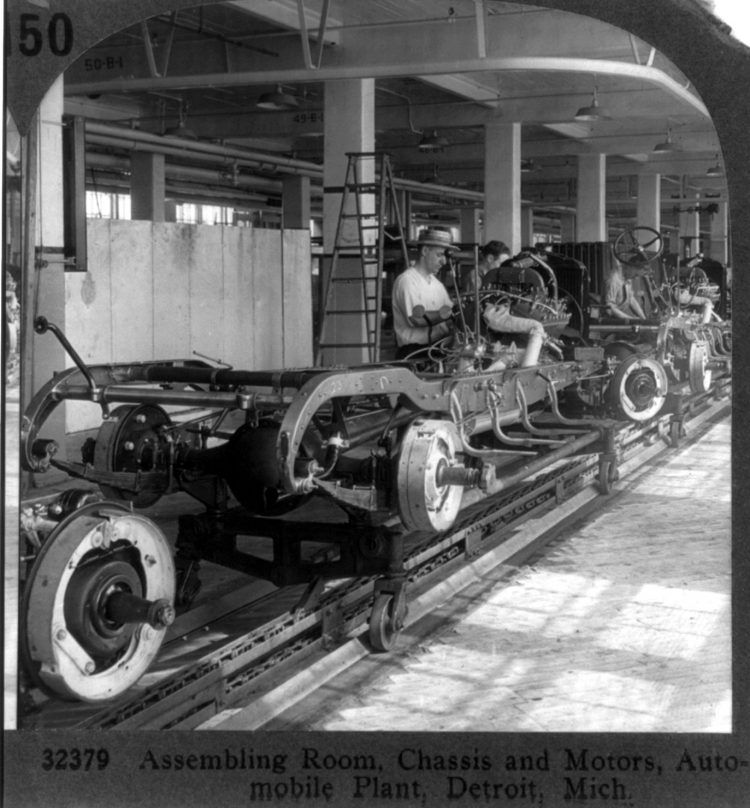
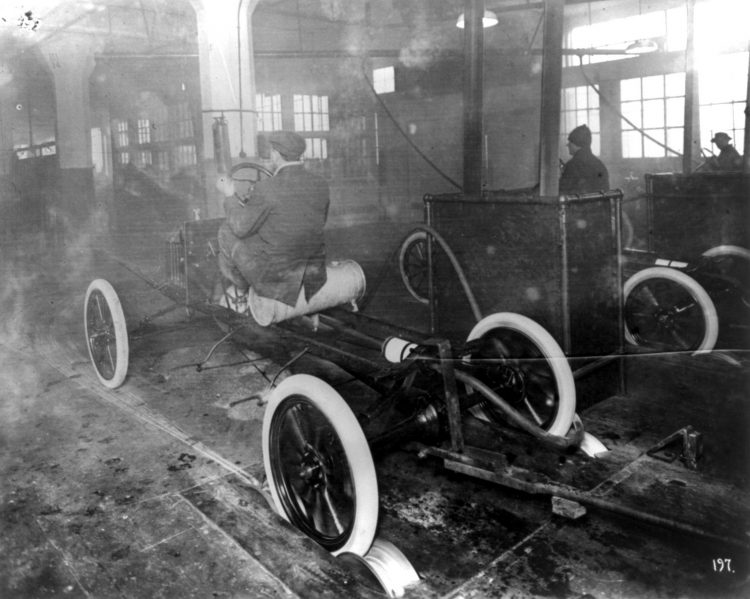
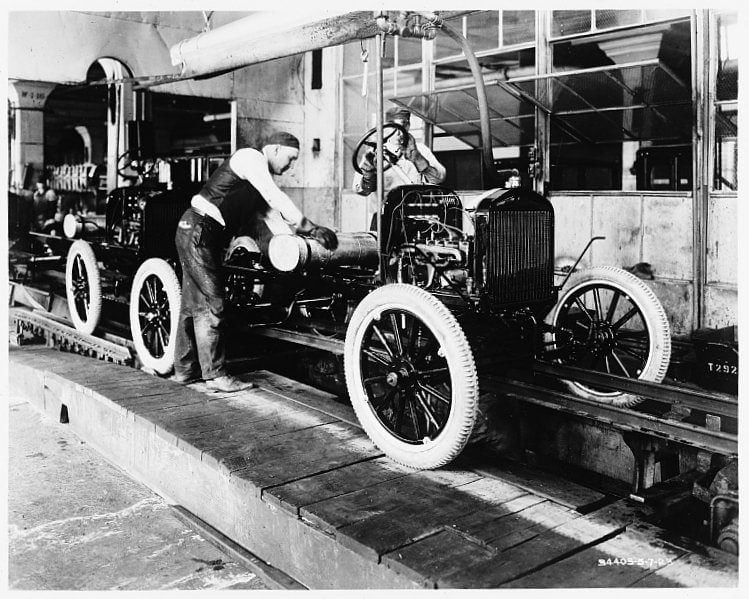
At the northern end of the chassis assembling lines, the rear wheels of the completed assembly drop on the friction driving pulleys beneath the floor, the rear axles revolve, driving the motor, which starts under its own power, the chassis becomes alive, and, turning the corner, runs out into John R Street, is driven a few turns up and down, and then, it the driver is satisfied with its performance, is headed to the train-loading platform, to begin its fledgling battle with the highways and byways of the earth.
The assembling lines of the Ford chassis have been undergoing constant changes ever since they came under the writer‘s observation in December last; the first method was to place the wheels under the chassis frame as soon as the axles were fixed in place and to push the chassis in course of assembly along the floor on its own wheels.
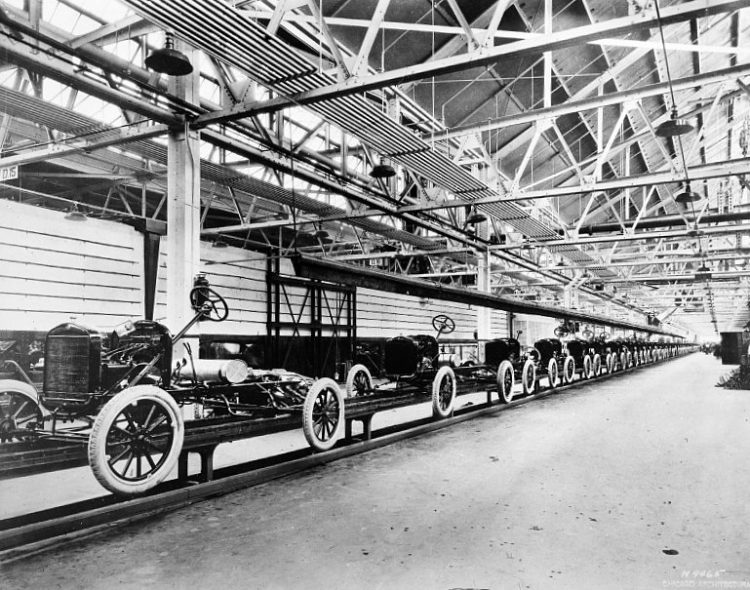
The most recent installation, and by far the best employed, provides metal ways on which to slide the chassis and it is drawn along by a slow-moving endless chain and takes the wheels only after the assembly is complete and when the chassis is ready to drop onto the starting friction pulleys.
It seems a very strange thing to say in the face of all the elaborately specialized multi-spindle machine tools shown in the Ford shops, that the really most important feature or these shops, and one which, so far as the writer has been able to learn, is entirely original with the Ford shops, is the providing of smooth metal ways on which work in process of assembling can be readily moved along.

Mr. Ford had the basic idea of straight-line chassis assembling several years ago, but the crush of endeavor to build cars enough to supply the demand caused various expedients in the way of oval path chassis assembling to be tried, then came a partial realization of the straight-line chassis assembling, in which the wheels were placed under the chassis as soon as the axles were ready to take them and the remainder of the straight-line travel was made on the chassis wheels.
Various improvements followed, but it was only in the last days of February, 1914, that two lines of high rails were placed on which the endless-chain driven chassis slides on the rails which support the chassis axles, all in precisely the same general manner as the motors are supported while being assembled.
Since the advantages of sliding motor support had been fully demonstrated long before the straight-line-path chassis assembling was begun, it seems that the double rail and chassis sliding should have been the first thing tried, but it was only after many other means of chassis support in the assembly line had been tried that the high rails chassis support was installed.
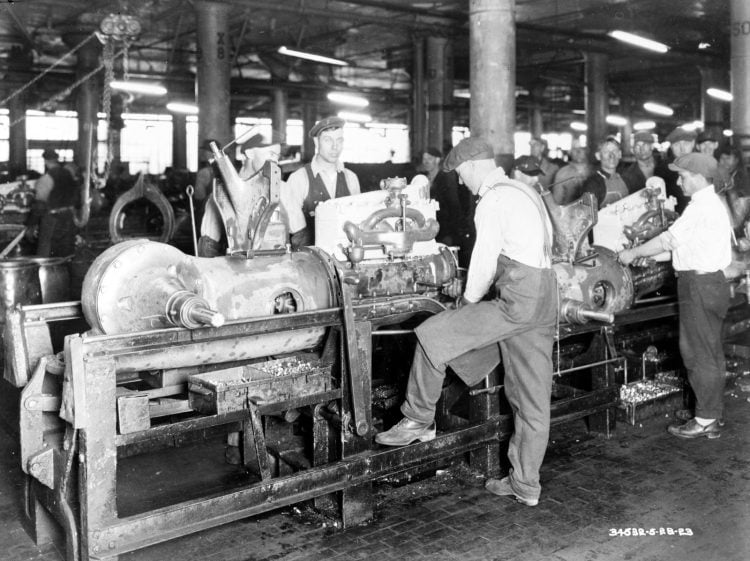
This fascinating scene of rapid, varied and seemingly unguided, yet wholly harmonious and orderly effort, holds the interest of the visitor, watching each new addition to the assembly with the keenest interest the entire spectacle is unlike any other industrial scene whatever, and really gives the sensation of witnessing the Frankenstein-like creation of a newly-formed, living and moving independent existence.
The 4 o’clock quitting bell finds the yet keenly interested visitor standing at the north end of the assembling lines, where a new chassis is vivified a thousand times in every eight-hour day, and hurries out through the factory doors as if eager to begin its own work in the world—a truly unique scene of fascinating interest, which holds the observer spellbound.
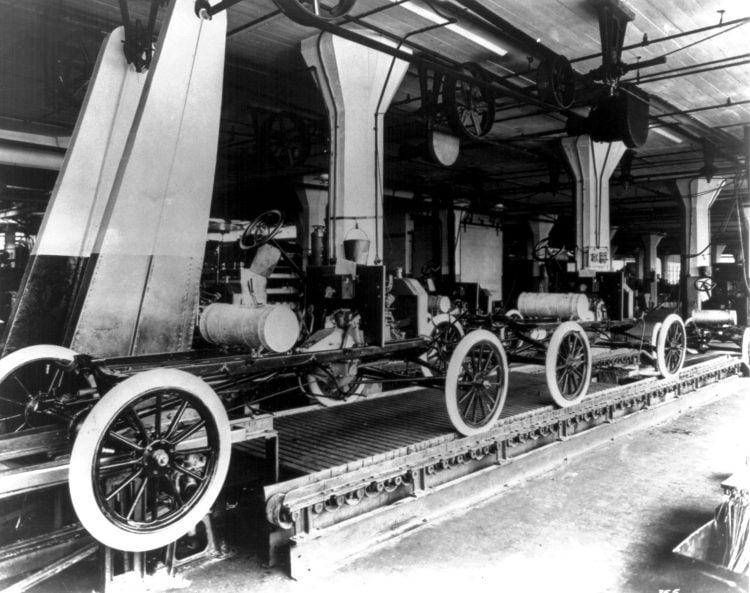
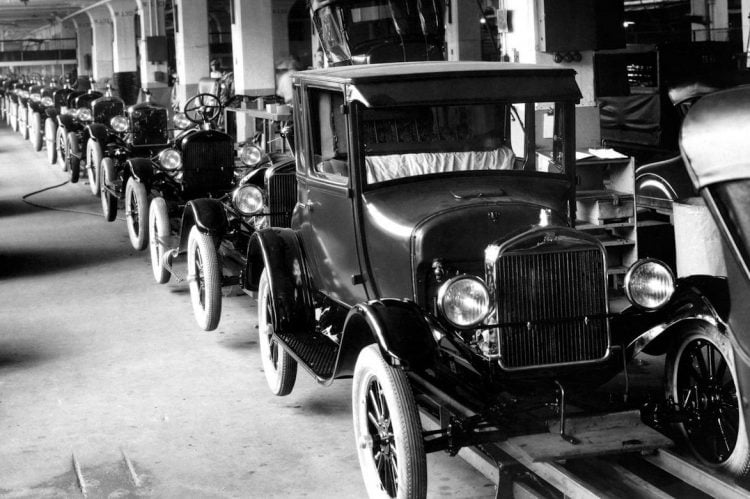
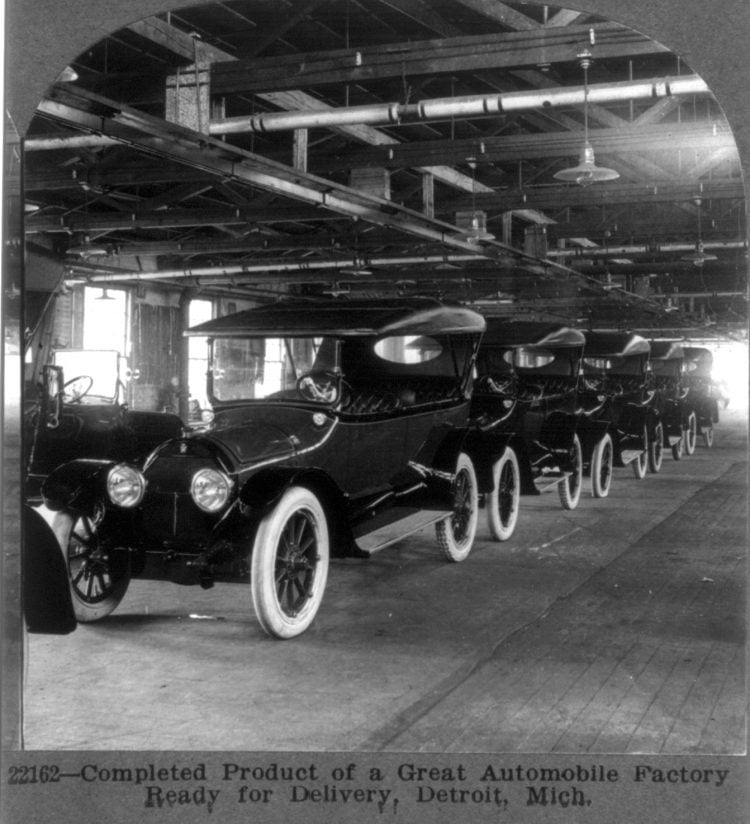
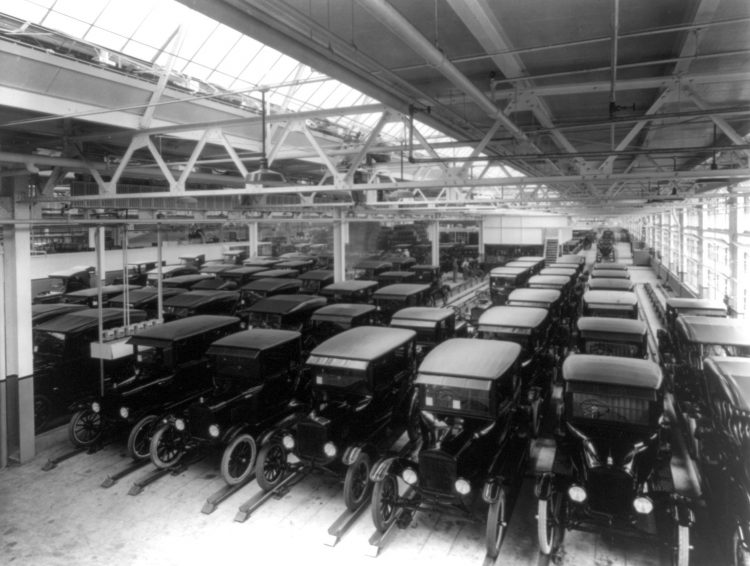