From the Pantheon to skyscrapers: Modern concrete rises through the ages
Modern concrete has massively changed the shape of the world for over one hundred years, but in its more primitive form, it’s a centuries-old combination of rocks and minerals.
By mixing lime — smashed and burned limestone rock — with sand, rocks, and water, even prehistoric cultures were able to create a mortar-like cement as early as about 1300 BC.
A super-strong version, now known as Roman Concrete, was made by combining limestone and volcanic ash with sea water.
Rome’s famous landmark, the Pantheon, was crafted out of this sort of concrete, and looks pretty amazing even almost 2000 years after its construction.
Portland cement was a game changer
Although the words are often used interchangeably, cement and concrete are not the same. Cement, like Portland cement, was a key innovation of concrete in the mid-19th century. Portland cement, combined with water and aggregate (including sand), makes up the modern concrete still commonly used in construction to this day.
And by the second half of the 19th century, when Francois Coignet found that combining concrete with steel rods significantly increased the support and stability of concrete structures, a wide range of applications for modern concrete was born — from chimneys and retaining walls to bridges, homes, skyscrapers and more. Since then, concrete construction has never been the same!
Modern cement was a revolutionary building material
In 1906, the world was taken in by the potential for this latest wonder of the Industrial Age — and Technical World Magazine wrote up a fascinating story about it (read on!).
Later yet, the clean structural lines concrete offered appealed to now-famous architects like Frank Lloyd Wright, as well as home buyers who appreciated the mid-century modern aesthetic of the post-war era.
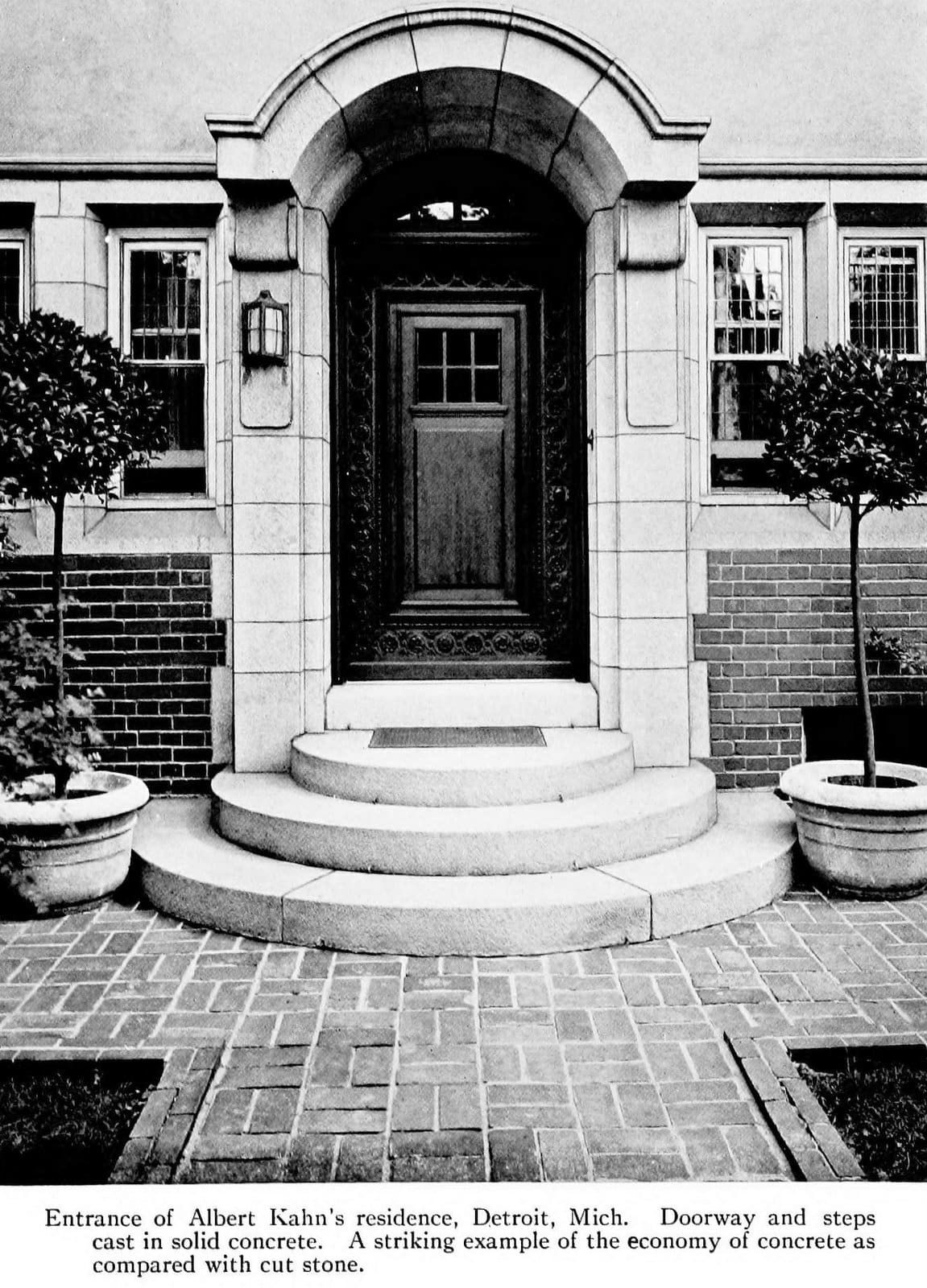
The hot new building material: Concrete (1906)
Economics and conveniences of concrete
Concrete is the new medium of the engineering wonder-worker. First, he builds the gaunt steel skeleton of a skyscraper, with a wooden mold of the desired width about the thin steel girders, writes D. M. Harper, in the Technical World Magazine.
Into this mold, he forces the liquid stone, and waits a few hours for it to harden. Then the wooden shields are removed, and there stands a smooth wall, which grows harder with the passage of each day and will withstand a greater pressure than granite or steel itself.
Or he builds a great bridge, leaping a hundred and fifty feet at a single span, of slender steel rods, forces concrete inside the temporary wooden skin which marks the desired shape, and has, next morning, a structure of strength and beauty, which will defy all the power of winds and waves alike.
Or, where twenty years ago, a tall chimney would have been laboriously built up, brick by brick, and a dozen feet in thickness at the base, he spins his steel spider-web, pours his liquid stone into a thin shell of less than a dozen inches, and behold a slender structure towering hundreds of feet into the air, and strong enough to stand anything short of a cyclone!
Many types of buildings with concrete
Skyscrapers, sidewalks, bridges, fence posts, dams, roofing tiles, telegraph poles, railroad ties, residences, piles, chimneys — these are a few of the uses to which concrete has been successfully put within the last few years.
In 1890, the total production of Portland cement in the United States was 335,000 barrels. Last year, over 30,000,000 barrels were produced — an increase of nearly 10,000 percent, in fifteen years. That marks the growth of the concrete industry in the same period — for cement is the essential element in concrete.
Yet, let modern constructing engineers take too much credit to themselves for the miracles they have accomplished, it may be well to remind them that the ancient Romans, in 27 BC, built of concrete the famous Pantheon, which is still one of the sights of the Imperial City, and the splendid dome of which is practically a solid concrete shell. Surely no building material could hope for a better demonstration of its durability than that.
Demanded by necessity
Portland cement is the basis for concrete as the moderns know it. And in that case, once again, the necessity of an ingenious engineer was the mother of invention.
One hundred and fifty years ago, an English engineer, John Smeaton, in attempting to construct a lighthouse upon Eddystone Rocks, found the need of a cementing material which would harden under water, and which would also develop an ultimate strength greater than that of ordinary lime.
Through a course of experiments, he discovered that an impure, soft, clayey limestone, when burned, possessed the property of “setting” — becoming hard — under water.
This was the beginning of hydraulic lime; and out of it grew the invention of true Portland cement, which is the finely pulverized product obtained after burning to the point of incipient fusion an intimate and properly proportioned mixture of calcareous and argillaceous material — in other words, limestone or marl, and clay.
In addition to Portland cement, there are also slag or pozzolana, and natural or Rosendale cements. Portland cement — so called from its resemblance to the stone found on the island of Portland off the coast of England — on account of its higher and more uniform quality, is the material usually considered in speaking of concrete.
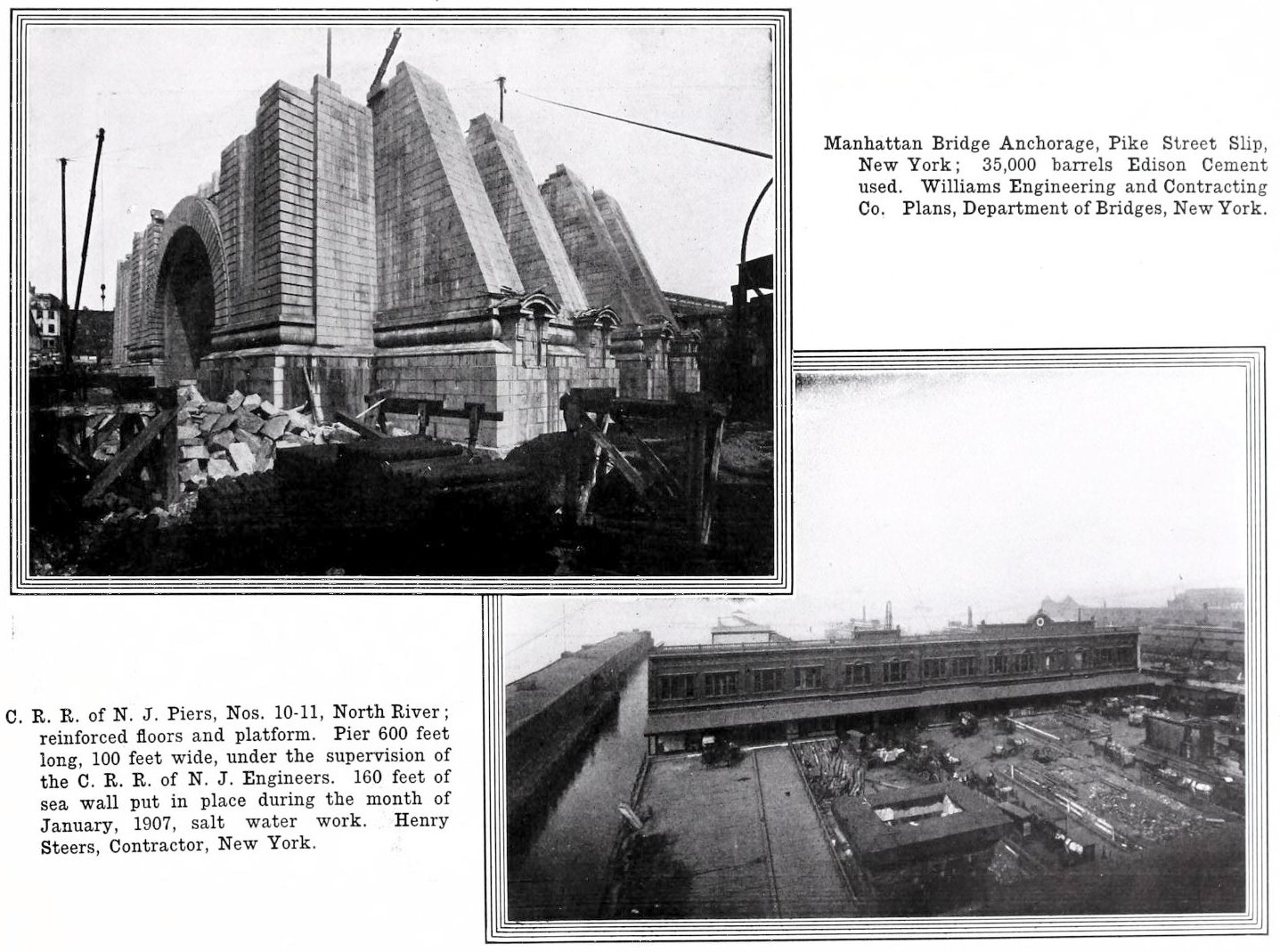
A belt of modern cement around the earth
Fifteen years ago, concrete was used principally for foundations and sidewalks. It is estimated that during these fifteen years, enough concrete walks have been laid to girdle the earth a dozen times. They are more easily laid than walks of natural stone, and are more attractive and durable.
But the day when concrete was only tramped underfoot went by several years ago.
Out at Butte, Montana, where the great stamping mills and ore-concentrating works have turned the mountain city into a titanic inferno of tall chimneys, belching black and sulphurous fumes, stands one tremendous tower, the top of which is 350 feet above the ground.
When its erection was planned, the first idea was to build it of brick. That would have required a thickness of twelve or fifteen feet of masonry at its base. But the matter was greatly simplified by the use of concrete.
Using modern concrete as a building material
Less spectacular, but far more important and general, is the use of concrete as a building material. The industry of making concrete building blocks has become a very large one within the last five years, and in almost every city and town can be found residences and business blocks built of this material.
The growing scarcity and increasing price of lumber make it certain that concrete will be more and more generally used for building purposes.
Very artistic residences are built of concrete building blocks. They are very comfortable, being cooler in summer and warmer in winter than buildings constructed of other materials.
The more common type of concrete building block is what is commonly known as the “one piece” system, usually 24 or 32 inches long by 8 inches high and 8, 10 or 12 inches in width, according to the thickness that is desired.
One or more vertical air-spaces, amounting in most cases to 33-1/3 percent, are provided. This not only lightens the block, but prevents the moisture from the outside from striking through, as well as from condensing on the inside, as in often the case with a solid wall. It is customary to plaster these hollow walls directly upon the inside of the block, and while there have been in a few cases undesirable work due to a lean and porous concrete, in general, satisfactory results have been obtained.
It is possible to make from concrete an absolutely impervious product by carefully selecting the aggregate of different-sized grams and then using enough cement to fill the voids. Another noticeable feature is that concrete becomes more impervious to water with age, as is the experience not only with concrete blocks, but with reservoirs, stand-pipes and similar structures.
Another class of these building blocks is what is known as the “two-piece” system, by which an absolutely hollow wall can be made. In general, these blocks consist of a comparatively thin longitudinal section, with one or more laterally extending arms which serve for binding the blocks together; or the wall may be made of two sections of plain veneer blocks bonded by metal wall-ties.
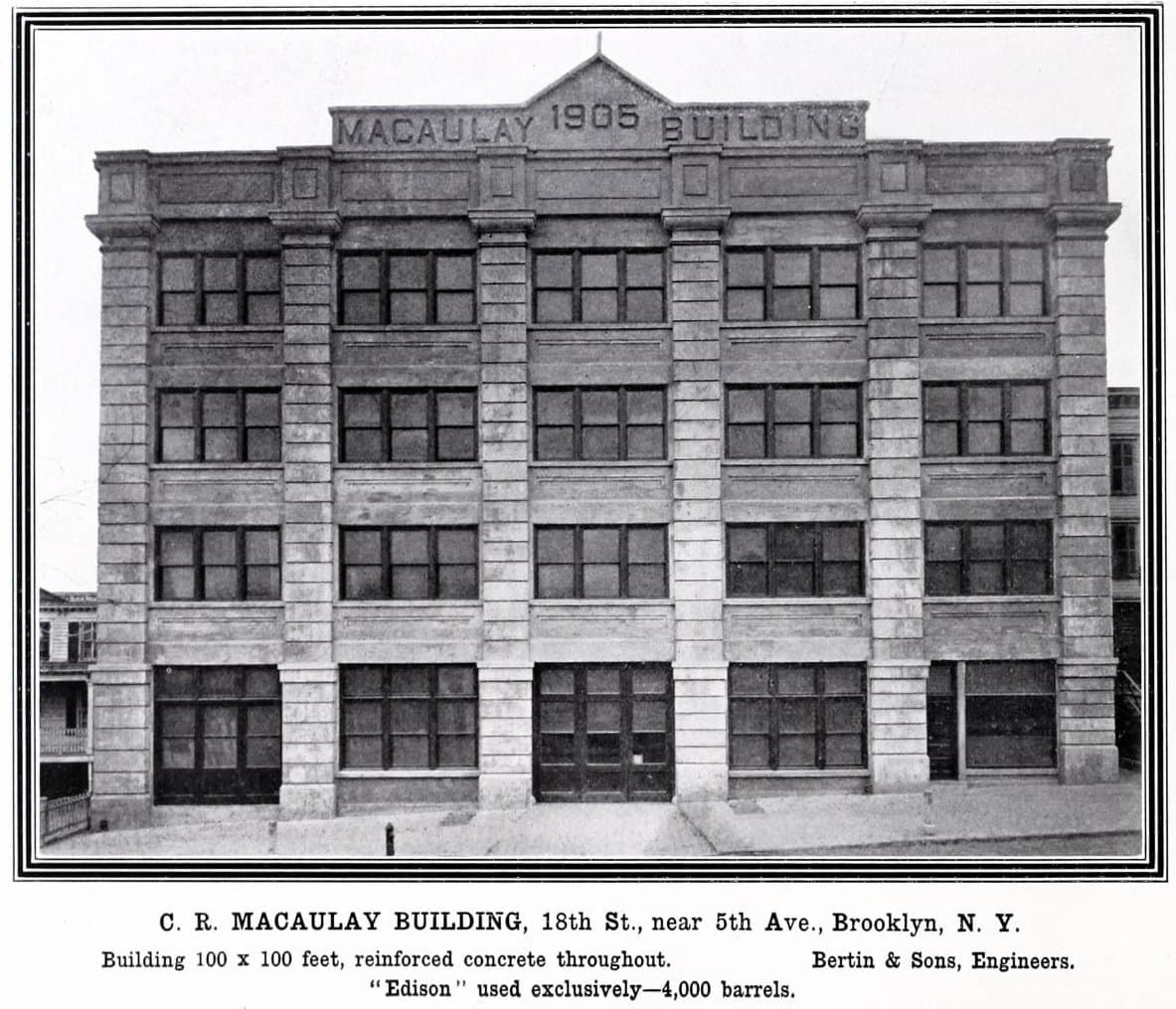
The coat of a concrete block building is considerably less than that of brick construction, and but little more than that of the frame. In fact, in one or two cases, the writer has known of concrete block buildings being erected at a lower cost than an ordinary frame construction.
The next class of concrete buildings to be considered are of the reinforced monolithic construction, which is now superseding almost entirely mill and steel frame construction for factories and warehouses and also for office buildings.
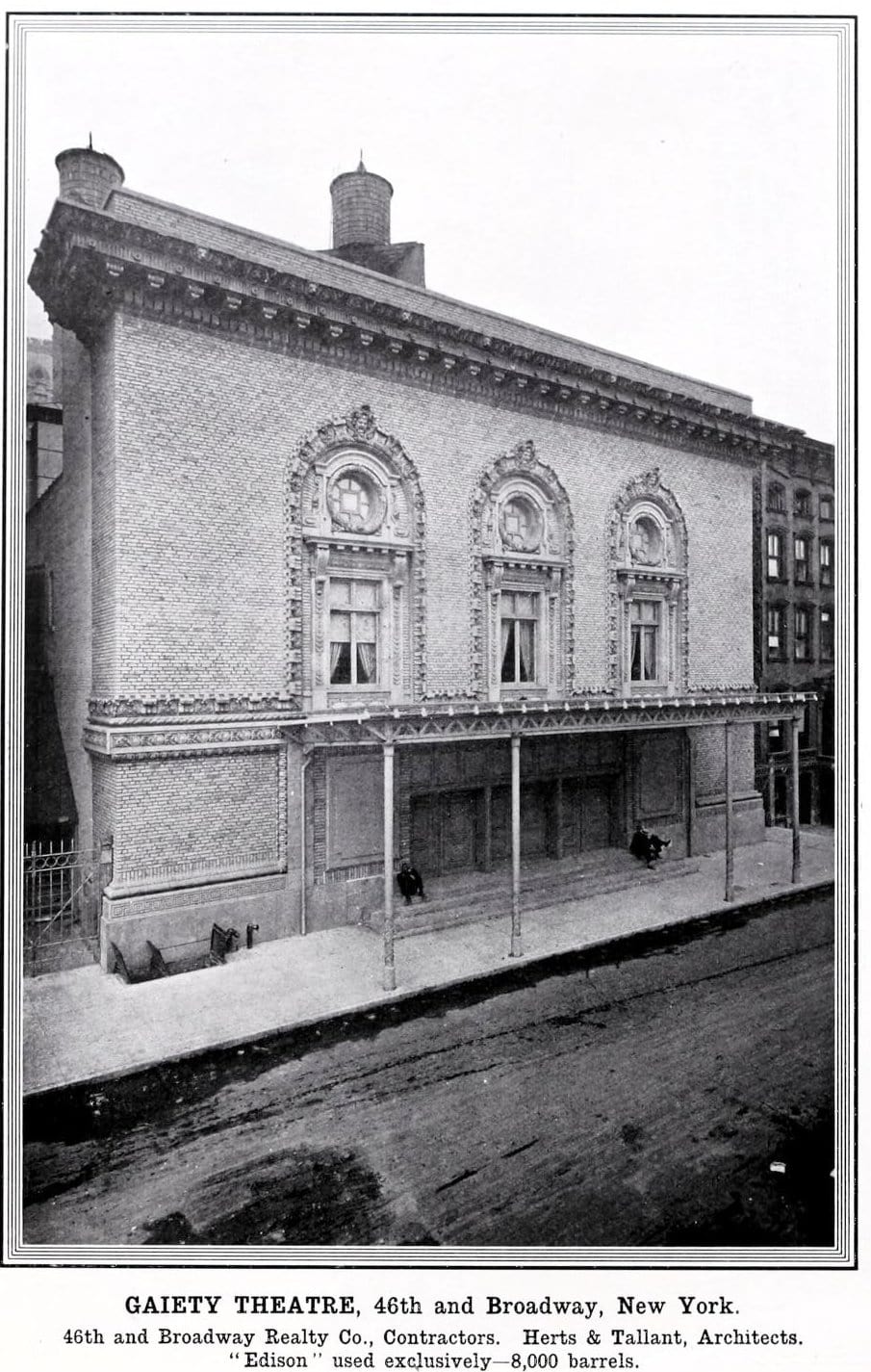
The principle of reinforced concrete as applied to buildings and bridges dates back for more than twenty years. The combination of steel and concrete, because of the adhesion between the two materials, amounting to about 500 pounds per square inch, as well as their almost equal expansion, has given us a building material far superior to either wood or steel.
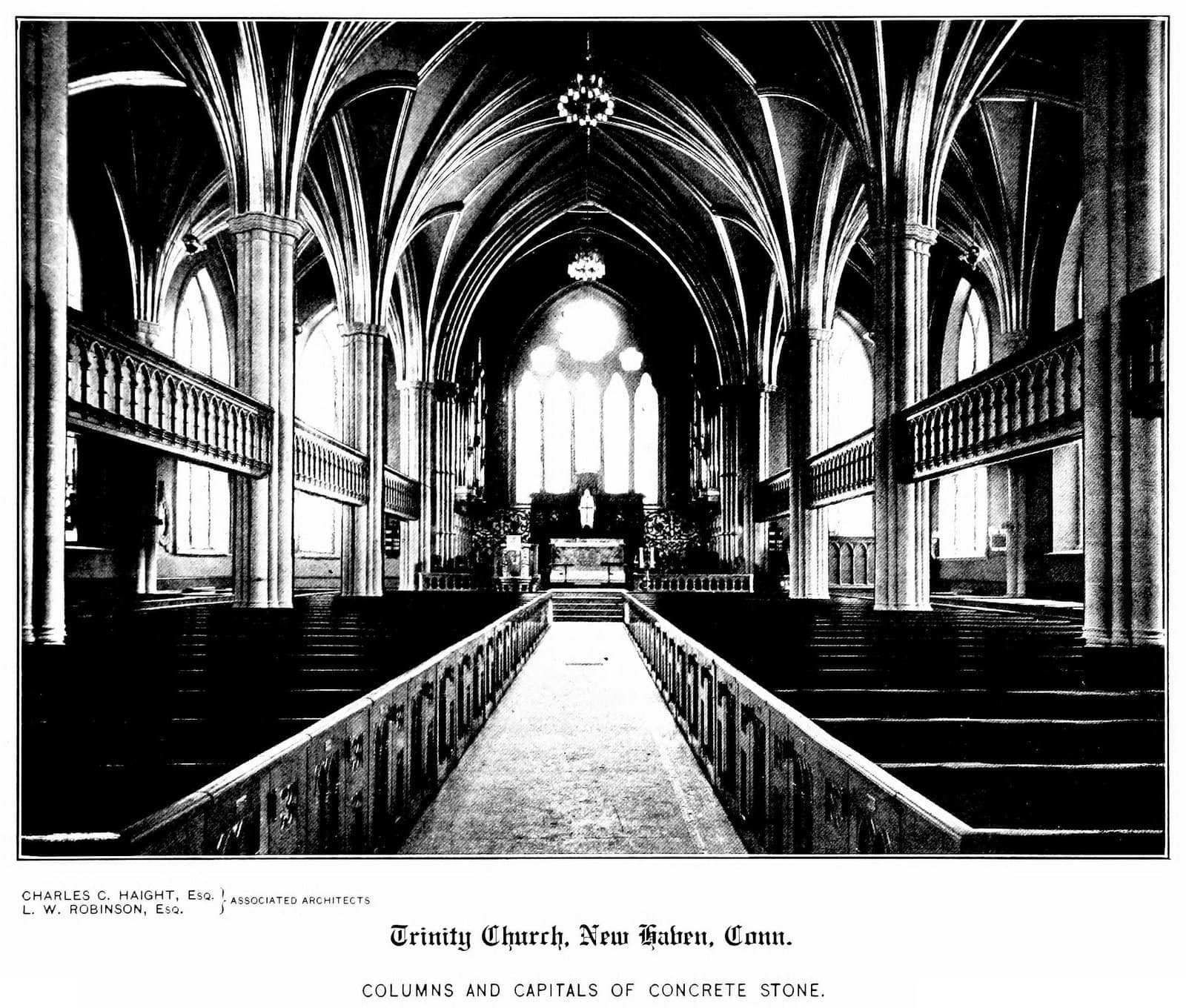